Good stocktaking practices
Preparation
Before starting a stocktake it’s important to establish the scope of what needs doing. Ultimately the goal of any stocktake is to keep accurate Stock on Hand, and to provide an accurate valuation of the store to owners, and regular stocktaking is considered good practice for any sized store.
The quickest way to establish the scope of the job ahead is to view your Stock Value Rejections report which is found in the Reports > Reports Central > Stocktake/ Value and Purchases tab
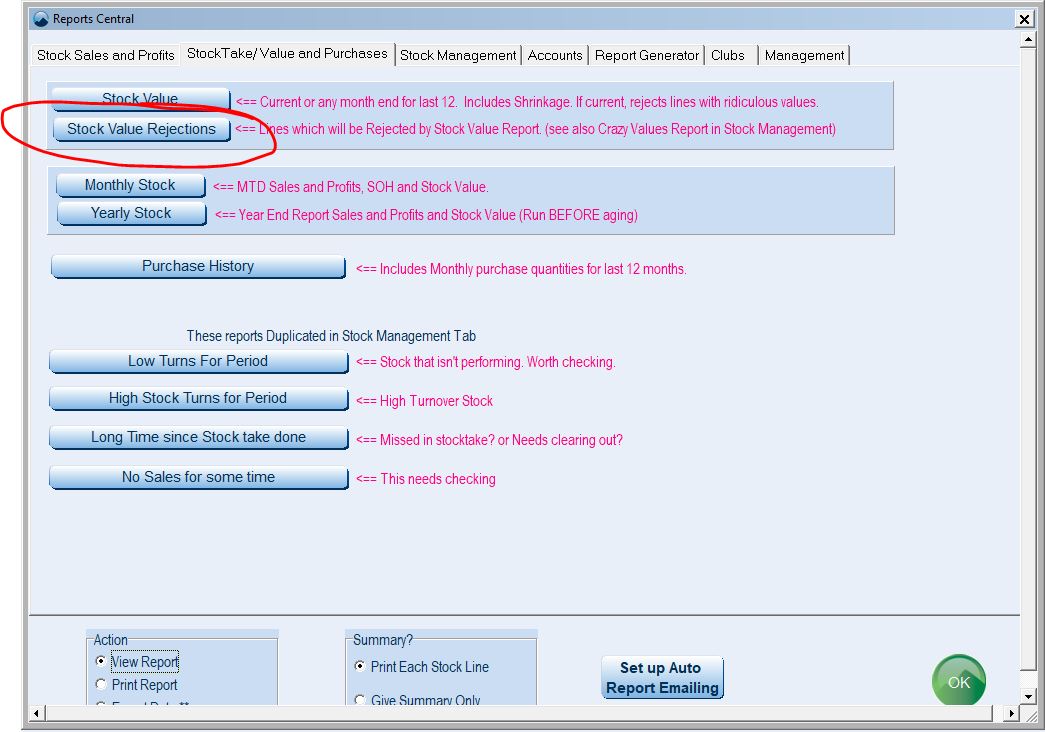
Read more about what and why we reject lines here.
The goal is to keep results in this rejections report to a minimum. If you have lots of results, then the scope of your stocktake would have to increase, potentially to a whole store stocktake.
Depending on how often you stocktake (if at all) you may decide to zero your SOH before starting. This means items which may have previously had SOH or fallen into a negative SOH figure and are no longer kept on the shelves will be zeroed and not contribute to your store’s valuation or rejections.
You can do this in the Point of Sale via Stock > Miscellaneous > Quick Stock Fixes and checking on “Zero Stock On Hand if long time since Stock Take“. Knowledge of filtering may be helpful at this stage.
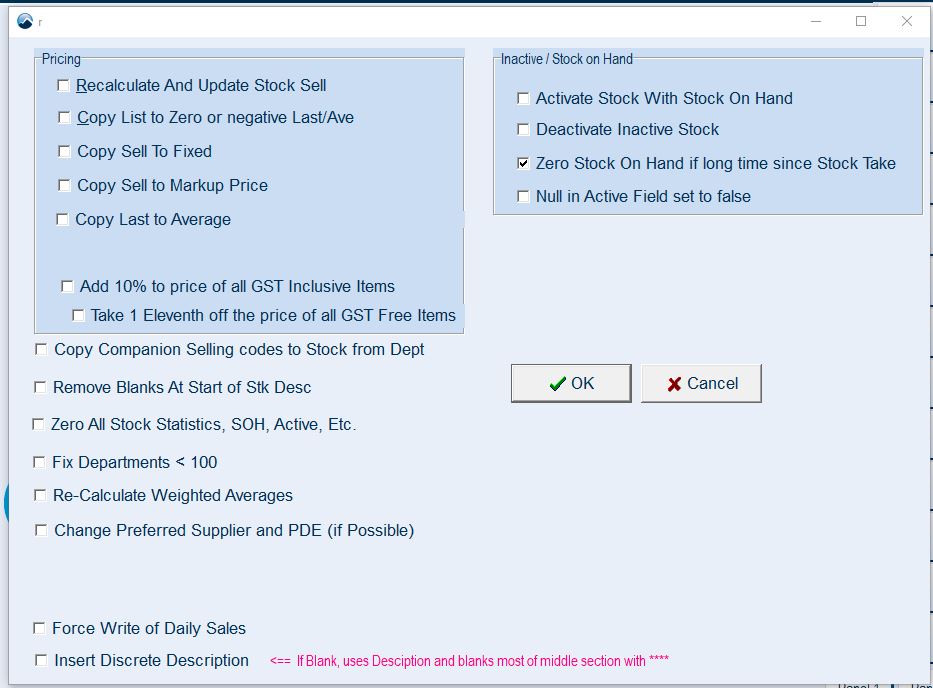
Target Lines
These are lines or sections of the store which should be stocktaken more regularly than others, or certainly monitored more often.
Examples of this might be areas of the store which are stolen from more often than others, items which are not sold regularly (i.e stock that isn’t performing) and expensive lines.
We can help you target some of these lines with reports from the POS.
In Reports > Reports Central > StockTake/ Value and Purchases tab, two useful reports to run are the “No Sales for some time” report and the “Low Turns For Period” reports.
Additionally the Stock Value Rejections report mentioned in the section above on preparation is effectively a list of high priority lines. All of these lines must be addressed.
The different ways to stocktake and their advantages
Wireless “At the shelf” Stocktake
The fastest comprehensive way to stocktake your store is to count stock at the shelves. This is a common stocktaking method we see used towards the end of financial years, and besides huge time savings, this stocktaking method also allows staff to face stock, account for missed shrinkage and renew pricing labels/ shelf tickets at the same time as stocktaking, so your store will look better for it! If you print pricing dates on your labels, it could also be a good time to readdress pricing for shop lines, particularly for lines which haven’t had a price change in a long time.
By design, this stocktaking method does away with any paperwork or formal structure. The stocktake doesn’t need to be done in any particular order, nor rushed through in a short time period. While all stocktaking in principle works better the quicker it can be done (as there is less chance for SOH drift to occur), you could reasonably stocktake in your spare time over a period of weeks or months.
Simply put, all your staff must do is count the items at the shelf and enter the quantities for each line. This can be done on our first to market tablet device. More info on our deals page.
Staff might stocktake one shelf or section at a time, or mark where they are up to with a sticky note or tag, ensuring they know what’s been counted and what hasn’t, should they get distracted or taken away to do other work while stocktaking.
Once counted, usage will continue deducting SOH, and invoicing will increment SOH appropriately. Alongside updating your shrinkage properly going forward, this method means your SOH should always remain fairly accurate (obviously things can still get stolen or get forgotten about!!)
It’s this mechanism which allows this method to have more-or-less no time requirement.
To wirelessly stocktake on our tablet, enter Tablet Mode with the button in the lower left of Point of Sale. Then scan an item, enter the quantity you have on hand, then scan the next item. You can scan the packaging barcode, the shelf ticket, or even PDE codes which are often provided on tickets that come from wholesalers or buying groups you might belong to. Additionally you can set items into Locations, Print labels, and set a Sell Price.
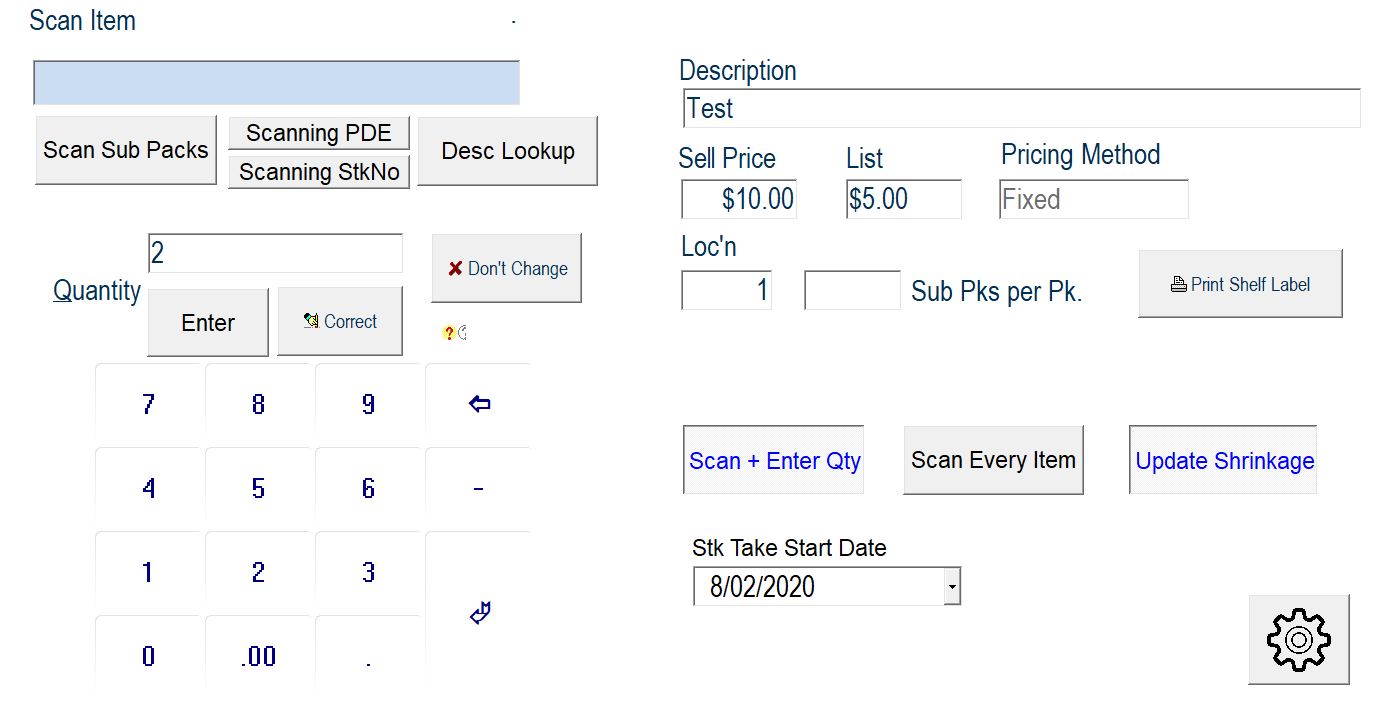
You can contact our sales team for more information about the Mountaintop Stocktaking Tablet.
Random Items Stocktake
This stocktaking method requires stock items to be brought to a workstation or till with Mountaintop Point of Sale installed, and as a result is often only used in particularly small stores or to address small sections of a store. It can also be used to compliment other styles of stocktakes, perhaps if you do not have wireless devices for all staff to use concurrently, this method allows other staff members to assist with the main stocktaking effort. Additionally this can be a good method for maintaining shrinkage, particularly at the very front of the store (where stock tends to get stolen from most but also where stores tend to keep a register).
Procedurally, it isn’t much different to the wireless stocktaking method elaborated on above. Count items, remember where you’re up to.
You can start randomly stocktaking in the POS via Stock > Stocktakes > Random Items Stocktake. Scan an item and enter the quantity, then scan the next line. Cancel when finished.
Structured Stocktake
This is an old style of stocktake, and we do no recommend it as it can seem complicated, particularly with junior staff (who are often tasked with stocktaking) and staff who haven’t much experience stocktaking. Additionally this stocktake has very strict time requirements, has multiple points where potential mistakes can be made by staff, and often takes more time than the above methods.
What the store does is produce a report of items kept in a section of the store, often by department or by location. Stock > Stocktakes > Easy Printout
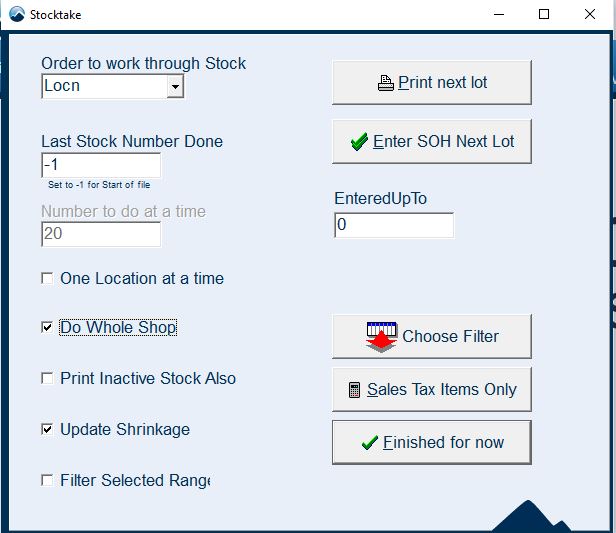
Enter your preferred method options, then click Print next lot. This will print you a report of target items. These items should then be stocktaken and their SOH figures written against the report.
The report wont print items in the order that you keep them in the shelves, so it can take some time to find items.
You then return to the computer and click the “Enter SOH Next Lot” button and enter the lines one by one.
Because of this, any SOH changes that occur between when the item is counted and when the figure is entered into the computer will not be recorded, which means this stocktaking method has a very strict time requirement.
Advantages of this method include the opportunity to check figures being entered at two points of time in the procedure, which may give some stores confidence in the figures being entered, as well as piecemealing the work out into smaller efforts, which can help focus work by staff.